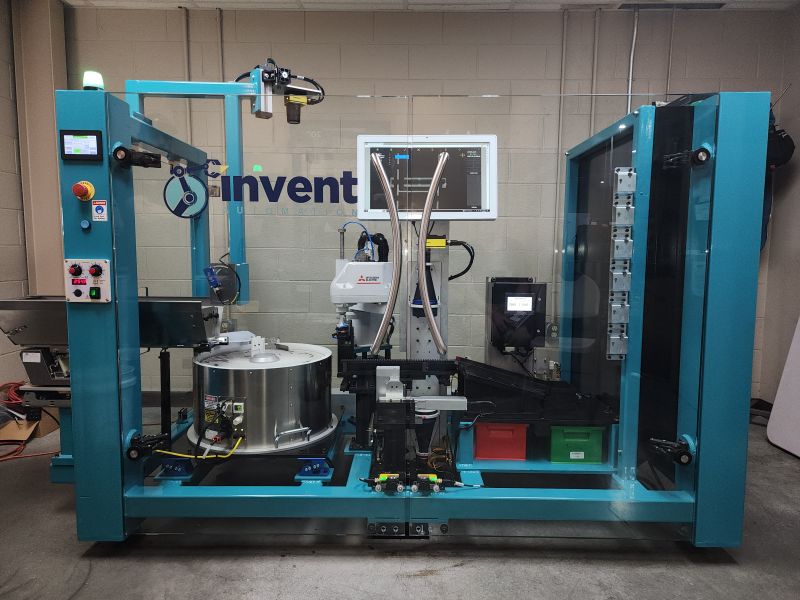
Invent Automation은 DENSO의 자동화에 따라 CapSen 비전 기술을 통합했습니다. 출처: 발명 자동화
자동차 제조는 오랫동안 로봇공학과 자동화의 사려 깊은 배치를 통해 이익을 얻었으며, 여기에는 그럴 만한 이유가 있습니다. 많은 복잡한 생산 공정 중에서 일부는 작업자가 안전하고 효율적으로 완료하기에는 너무 어렵거나 지루할 수 있습니다. 결과적으로 산업 자동화 기술은 OEM과 자동차 부품 공급업체 모두에게 다양한 방식으로 엄청난 가치를 더할 수 있습니다. 예를 들어, 선도적인 글로벌 자동차 부품 제조업체인 DENSO는 최근 육체적으로 힘들고 반복적인 운반물 처리 작업을 자동화하려고 했습니다.
직원들이 계속해서 페인트 부스에 무거운 토트 더미를 싣고 내리도록 하는 대신(그림 1), 회사 와 제휴 캡센 로보틱스3D 비전, 모션 계획 및 제어 소프트웨어를 작업에 맞게 맞춤화했습니다.
DENSO는 시스템 통합업체와도 파트너십을 맺었습니다. 자동화 발명 프로세스를 간소화하고 직원들이 더 가치 있고 육체적으로 덜 힘든 방식으로 공장 현장에 기여할 수 있도록 하는 시스템을 개발합니다. 이 활동은 팀 구성원과 회사 성과 개선을 위해 자동화를 통해 인간 작업을 보완하려는 DENSO의 광범위한 노력에 기여했습니다.
그림 1: 자동차 부품으로 가득 찬 크고 무거운 토트가 컨베이어 위의 페인트 부스로 운반되고, 여기에서 코봇이 자동화된 프로세스의 일부로 토트를 집고 배치합니다. 출처: 발명 자동화
DENSO에서 60초(미만)에 들어갔습니다.
DENSO 운영의 일환으로, 자동차 부품은 저광택 차콜색 페인트로 도색되어 시각적으로 표면을 매끄럽게 하여 더욱 깔끔한 외관을 구현하는 동시에 차량 내부의 빛을 흡수하고 눈부심을 줄여줍니다.
이전 설정에서는 직원들이 플라스틱 자동차 부품으로 가득 찬 6개의 토트를 컨베이어에 쌓은 다음 운영자에게 제시했고 운영자는 수동으로 부품을 제거하여 페인트 부스 스테이션에 넣은 다음(그림 2) 다시 토트에 포장했습니다. . 직원은 매일 30초마다 토트백을 쌓거나 뗐습니다.
이러한 반복적인 동작은 팀 구성원이 더 영향력 있는 작업을 수행할 수 있도록 하는 자동화 기회로 확인되었습니다. 그러나 작업 현장의 레이아웃 제약으로 인해 전통적인 형태의 자동화가 어려워지고 컴팩트하고 유연한 시스템이 탄생하게 되었습니다.
그림 2: 자동차 부품을 페인트 부스로 가져오면 표면을 매끄럽게 하고 차량 내부의 빛을 흡수하는 데 도움이 되는 저광택 페인트가 뿌려집니다. 출처: 발명 자동화
새로운 시스템을 사용하면 인바운드 컨베이어가 엔드 이펙터에 Intel RealSense 3D RGB 깊이 카메라가 부착된 6축 협동 로봇(그림 3)으로 도색되지 않은 물체의 토트를 운반합니다. 카메라는 로봇이 토트를 시각적으로 식별하고 집기 높이를 측정하는 데 도움이 됩니다.
그만큼 캡센 PiC 2.0 그래픽 처리 장치(GPU)가 장착된 산업용 PC에서 실행되는 소프트웨어를 통해 로봇은 계획을 세울 수 있습니다. 운동토트를 찾아 선택하고 조작한 다음 페인트 부스 스테이션으로 향하는 다른 컨베이어를 향해 이동합니다. 그곳에서 부품을 내려서 칠하고 경화를 위해 오븐에 넣은 다음 검사한 후 토트에 다시 넣고 로봇을 향해 돌아가는 컨베이어에 다시 넣습니다. 로봇은 토트를 식별하고 아웃바운드 컨베이어에 배치합니다.
그림 3: DENSO의 COBOTTA PRO 1300 협동 로봇, 참고용입니다. 출처: 발명 자동화
파트너는 기동성, 시력 문제를 해결합니다.
로봇이 충돌을 일으키지 않고 대형 토트를 집고 배치하려면 여러 축을 따라 정밀한 움직임이 필요합니다. CapSen PiC 2.0 시뮬레이션 환경을 통해 팀은 로봇의 기동성을 테스트하고 모든 것에 접근할 수 있는지, 로봇이 어떤 것과도 충돌하지 않는지 확인할 수 있었습니다.
그러나 팀이 실제 시스템을 테스트했을 때 로봇이 토트를 집어들면 토트가 구부러지기 시작한다는 사실을 발견했습니다. 토트의 무게를 보상하고 컴팩트 셀 내에서 충돌 없이 유연한 움직임을 보장하기 위해 파트너는 시스템을 맞춤화하기 위해 노력했습니다.
“우리는 소프트웨어에 AI를 사용하여 로봇이 무작위 쓰레기통 따기, 머신 텐딩포장, 조립 및 운반물 처리”라고 CapSen Robotics의 CEO인 Jared Glover는 말했습니다. “어려운 애플리케이션, 특히 시뮬레이션 환경만으로는 충분하지 않은 애플리케이션의 경우 우리는 생산 작업에서 얻은 데이터를 기반으로 AI 알고리즘과 모델을 맞춤화합니다. 이를 통해 소프트웨어는 로봇의 모션을 최적화하여 로봇이 충돌 없이 자유롭게 움직일 수 있도록 하고 사이클 시간 내에 토트를 전달할 수 있습니다.”
DENSO의 토트 핸들링 프로젝트를 위해 CapSen Robotics는 먼저 AI 소프트웨어를 교육하여 토트 핸들을 감지하고 위치를 파악했습니다. RGB-D 카메라는 핸들의 이미지를 캡처하고 소프트웨어는 핸들을 감지하는 기계 학습 알고리즘을 실행하여 소프트웨어가 로봇의 동작 계획을 수행할 수 있도록 합니다.
로봇의 엔드 이펙터가 핸들에 배치되면 토트의 무게를 식별하여 로봇이 작동을 멈추거나 토트가 떨어지는 갑작스러운 움직임을 일으키지 않도록 해야 합니다. 저울을 사용하는 대신 CapSen의 소프트웨어는 모터의 토크 값을 분석하고 이 값을 사용하여 피킹할 무게를 결정합니다.
DENSO의 생산 엔지니어인 Kevin Peek는 “로봇의 토크 감지를 사용하여 무게를 파악하고 토트가 픽업되었는지 확인하는 것은 CapSen이 시스템에 추가한 귀중한 포카요케였습니다.”라고 말했습니다.
게다가 어떤 기계는 비전 시스템을 설계하고 설치하는 동안 문제가 발생했지만 협업 팀은 이러한 문제가 발생하지 않도록 협력했습니다.
Peek는 “토트 스택에는 최대 6개의 토트가 포함될 수 있으므로 시스템이 적절한 스택을 보장해야 했습니다.”라고 말했습니다. “토트가 2개만 있으면 문제가 덜할 수 있지만, 토트가 6개 쌓여 있는데 하나가 제대로 중첩되지 않으면 스택 전체가 넘어져 작업에 큰 지연이 발생할 수 있습니다.”
이 과제를 해결하기 위해 시스템은 로봇이 토트를 스택에 놓으면 로봇이 약간 뒤로 이동하여 카메라로 스택을 볼 수 있도록 설계되었습니다. 소프트웨어의 기계 학습 알고리즘은 시스템이 두 개의 토트 사이의 간격을 찾아 적절한 적재를 보장하는 데 도움이 되었으며, 소프트웨어는 또한 스택의 정확한 토트 수를 계산하고 확인했습니다.
DENSO는 낙하물 없음, 픽업 누락 없음 보고
궁극적으로 CapSen PiC 2.0 소프트웨어의 다양성으로 인해 이 소프트웨어가 이 프로젝트의 소프트웨어 솔루션으로 선택되었습니다. 왜냐하면 최종 사용자가 다양한 시스템 하드웨어 부분에서 나오는 모든 데이터를 완전히 사용할 수 있기 때문입니다. 이는 프로그래밍 가능 논리 컨트롤러(PLC)를 사용할 때와 같이 기본 프로그래밍을 통해 작업하는 대신입니다. 이 애플리케이션에서는 캐비닛에 PLC가 없습니다.
그림 4: CapSen PiC의 직관적인 HMI는 시스템 상태를 표시하고 작업 실행 프로세스를 단순화합니다. 출처: 발명 자동화
모든 것은 CapSen 인간-기계 인터페이스(HMI)에서 처리됩니다. 운영자는 이를 사용하여 기계를 제어하고, 로봇 교정 정보를 얻고, 무엇보다도 카메라가 보는 내용을 시각화할 수 있습니다(그림 4).
사용자 인터페이스는 기술 지식이 없는 직원이 자동화나 엔지니어링 전문 지식 없이도 일상 업무의 일부로 시스템을 작동할 수 있도록 설계되었습니다.
또한 이 소프트웨어는 하드웨어에 구애받지 않으므로 DENSO에 특별한 이점을 제공했습니다. 실제로 시스템의 초기 테스트에는 모바일 조작여기서 자율 이동 로봇(AMR) 창고 전체에 토트 및 기타 컨테이너를 이동할 목적으로 시설 주변으로 로봇을 운반했습니다.
이 구성에서 CapSen의 소프트웨어는 AMR을 제어하고 좌표를 얻은 다음 AMR에 수정 지침을 보내 AMR을 흐름 랙 레인에 정렬합니다.
토트를 쌓고 내리는 것은 산업 환경에서 일반적인 응용 분야이지만, 이 시스템은 유연성을 염두에 두고 설계되었으므로 다른 응용 분야로 확장 또는 개조하거나 AMR을 사용하여 이동식으로 만들 수 있습니다.
또한 시스템이 설치된 이후 로봇은 토트 하나를 떨어뜨리거나 픽 하나를 놓치지 않았으며 DENSO 직원의 어깨에서 육체적, 은유적 무게를 모두 제거했습니다.
저자 소개
보 리들리 테네시 녹스빌의 수석 부사장입니다. 자동화 발명. 그는 이전에 DENSO에서 생산 엔지니어 및 기계 설계자로 근무했습니다. 이 사례 연구는 허가를 받아 게시되었습니다.
게시물 비전 기반 코봇으로 DENSO의 페인트 프로세스 자동화 처음 등장한 로봇 보고서.